Have you ever wondered what keeps the oil and gas industry running smoothly? Among many factors, the fabrication of pressure vessels plays a pivotal role. These vessels hold gases or liquids at a pressure significantly different from the ambient pressure, and their integrity is crucial for operational safety and efficiency. At the heart of pressure vessel fabrication lies a critical component: steel materials. Their strength, durability, and versatility make them indispensable in the construction of these high-stress containers. Whether you’re a professional in the steel fabrication industry or just curious about how things work behind the scenes, understanding the importance of steel in pressure vessel fabrication offers insight into the backbone of the oil and gas sector.
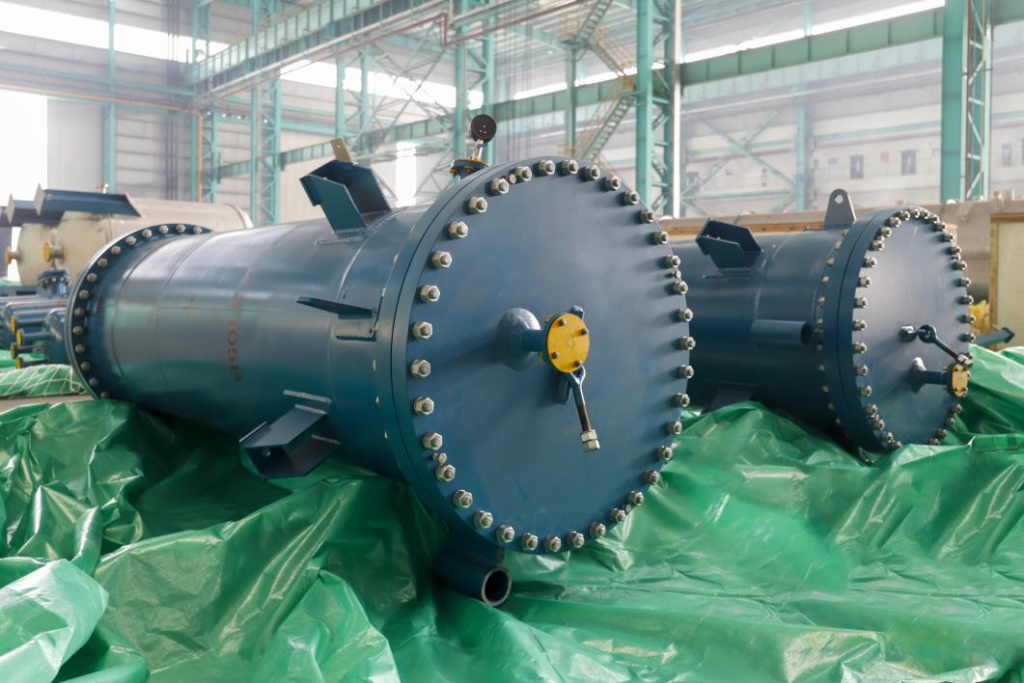
Characteristics of Steel Materials in Pressure Vessel Fabrication
In the world of pressure vessel fabrication, particularly within the oil and gas sector, the materials selected for the construction of these vessels must meet rigorous standards. The characteristics of these materials not only dictate the safety and reliability of the pressure vessels but also impact their efficiency and life span. Among the various materials available, steel stands out for its exceptional properties, making it a staple in the fabrication of pressure vessels.
Strength and Durability
One of the primary reasons steel is favored for pressure vessel fabrication is its remarkable strength and durability. Pressure vessels are designed to handle extreme conditions, including high pressures and temperatures, which require a material that can withstand such demanding environments without compromising its integrity. Steel’s high tensile strength makes it capable of resisting deformation under stress, ensuring that vessels maintain their shape and functionality even in the most challenging conditions. Moreover, steel’s durability means that pressure vessels made from this material can last for many years, making it a cost-effective choice for the industry.
Corrosion Resistance
Another crucial characteristic of steel in pressure vessel fabrication is its corrosion resistance. The oil and gas industry often involves the processing and storage of substances that can be highly corrosive, posing a significant threat to the integrity of pressure vessels. Certain types of steel, such as stainless steel, contain chromium, which forms a passive layer on the surface of the steel, protecting it from corrosion. This quality makes steel an ideal choice for pressure vessels that are exposed to harsh chemicals or environments, as it helps prolong the vessel’s life and maintain its structural integrity over time.
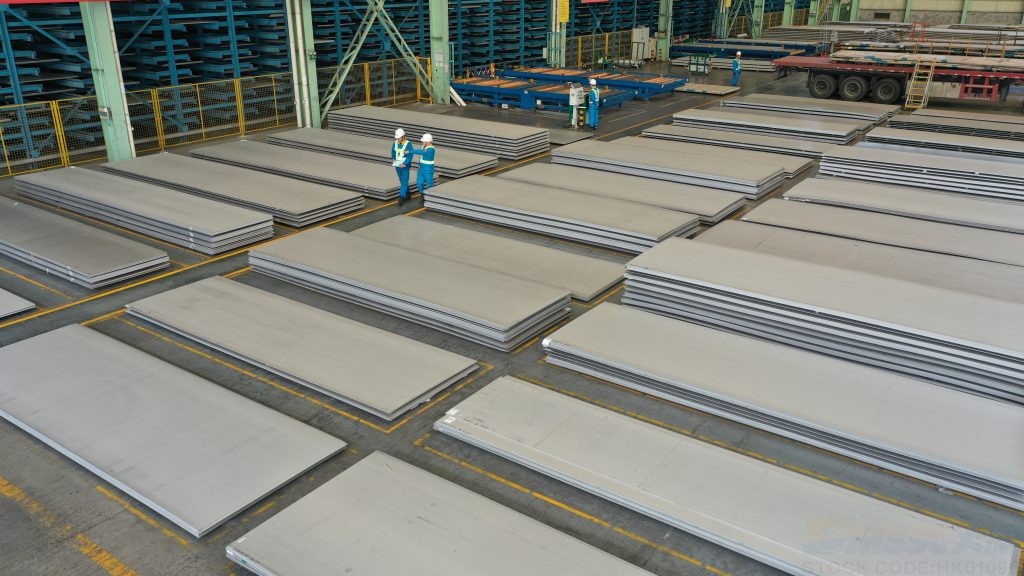
Steel Fabrication Processes for Pressure Vessels
The fabrication of pressure vessels from steel involves a series of processes, each crucial to ensuring that the final product meets the required specifications and safety standards. From welding techniques to heat treatment and quality control measures, the fabrication process is a meticulous one that requires precision and expertise.
Welding Techniques
Welding is a pivotal part of the steel fabrication process for pressure vessels, as it involves joining the steel plates and components together to form the vessel. The welding technique used must be suitable for the type of steel and the specific requirements of the pressure vessel. Common welding methods include:
– Shielded Metal Arc Welding (SMAW): Also known as stick welding, this method is versatile and widely used, suitable for many types of steel.
– Gas Tungsten Arc Welding (GTAW): Known as TIG welding, this technique offers high precision and quality, ideal for welding thin sections of stainless steel.
– Gas Metal Arc Welding (GMAW): Or MIG welding, this method is faster than TIG welding and is effective for welding thicker steel sections.
Each welding technique has its advantages and specifics, making the choice of method a critical decision based on the design requirements of the pressure vessel.
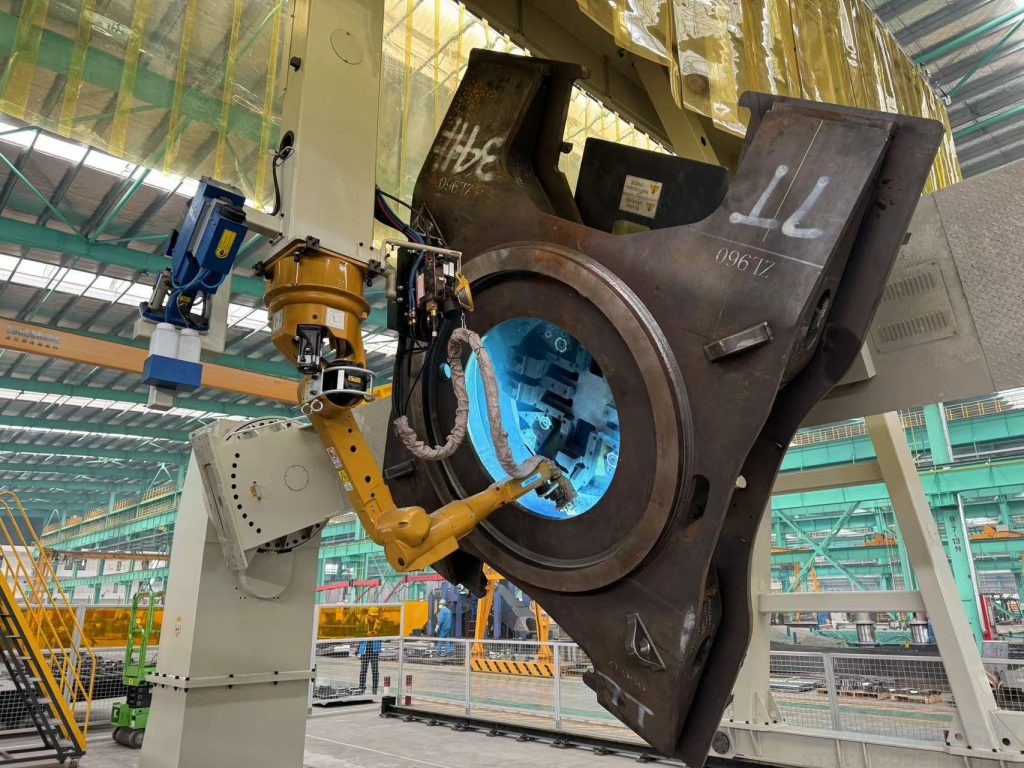
Heat Treatment Methods
After welding, steel pressure vessels often undergo heat treatment, a process that enhances the properties of the steel, making it more suitable for its intended use. Heat treatment can relieve stresses introduced during welding, improve toughness, and increase resistance to corrosion and wear. Common heat treatment methods include:
– Annealing: This involves heating the steel to a specific temperature and then cooling it at a controlled rate to reduce hardness and improve ductility, making the steel easier to work with.
– Normalizing: Similar to annealing, this process heats the steel above its critical temperature and then allows it to air cool. This results in a more uniform microstructure, enhancing strength and toughness.
– Quenching and Tempering: In this process, steel is heated and then rapidly cooled (quenched) in water or oil, followed by reheating it to a lower temperature (tempering). This process increases the hardness and strength of the steel.
Quality Control Measures
Ensuring the quality of steel pressure vessels is paramount, necessitating strict quality control measures throughout the fabrication process. These measures include:
– Material Inspection: Before fabrication begins, the steel materials are inspected for quality, ensuring they meet all necessary standards and specifications.
– Welding Inspection and Testing: After welding, inspections are conducted to check for flaws or defects in the welds. Various testing methods, such as ultrasonic testing, radiographic testing, and magnetic particle inspection, can be used.
– Final Inspection and Testing: Once the fabrication process is complete, the pressure vessel undergoes a final inspection and testing phase. This includes hydrostatic testing, where the vessel is filled with water and pressurized to ensure it can safely hold the maximum operating pressure.
Quality control is an ongoing process that encompasses every stage of fabrication, from the initial selection of materials to the final delivery of the pressure vessel. It ensures that the vessels not only meet the required standards but also cater to the safety and reliability demands of the oil and gas industry.
In conclusion, the characteristics of steel materials, combined with meticulous fabrication processes and stringent quality control measures, make steel an indispensable material in the construction of pressure vessels. Its strength, durability, and corrosion resistance align with the requirements of the oil and gas industry, ensuring that pressure vessels fabricated from steel can withstand the rigorous conditions they will face.
Importance of Steel Materials in Oil and Gas Industry
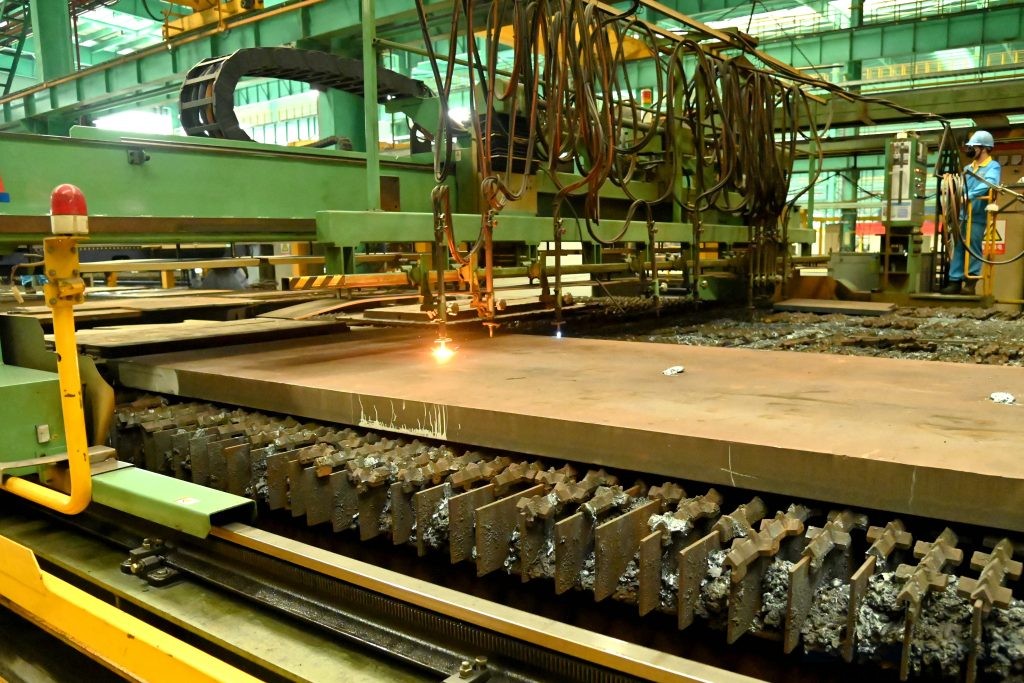
Steel is an incredibly versatile and durable material, making it indispensable in various industries. In the context of the oil and gas sector, steel is particularly critical due to its unique properties, which are tailored to meet the rigorous demands of extracting, processing, and transporting these natural resources. Let’s delve into why steel materials hold such a pivotal role in the oil and gas industry, focusing on its use in pressure vessel fabrication.
Steel’s inherent qualities, such as its high strength, flexibility, and resistance to corrosion, make it the ideal choice for constructing pressure vessels. These vessels are essential for storing and processing gases and liquids at high pressures, which are common conditions in oil and gas operations. The ability of steel to withstand these extreme environments without failing is paramount for the safety and efficiency of industrial operations.
Strength and Durability
One of the most valued properties of steel in the oil and gas industry is its exceptional strength and durability. Pressure vessels are subjected to harsh operational conditions, including extreme pressures and temperatures. Steel’s ability to maintain its integrity under these conditions, without deforming or cracking, is essential for preventing accidents and ensuring the continuous operation of facilities. High-strength steel grades, specifically designed for pressure vessels, can endure these conditions for prolonged periods, thus ensuring the longevity and reliability of the equipment.
Corrosion Resistance
Another critical aspect of steel that makes it suitable for the oil and gas industry is its resistance to corrosion. Corrosive substances, such as crude oil, natural gas, and seawater, are commonplace in oil and gas operations. Certain steel grades are specifically engineered to withstand these corrosive environments, either through the addition of alloying elements that enhance their corrosion resistance or through the application of protective coatings. This corrosion resistance is crucial for maintaining the structural integrity of pressure vessels and avoiding costly leaks or failures.
Flexibility in Fabrication
The adaptability of steel materials in terms of fabrication is a significant advantage in the construction of pressure vessels. Steel can be molded, cut, and welded into various shapes and sizes, allowing for the custom fabrication of pressure vessels to meet specific operational requirements. Advanced manufacturing techniques, such as automated welding and precision machining, further enhance the quality and efficiency of steel fabrication. This flexibility not only accommodates the diverse needs of the oil and gas industry but also enables innovations in pressure vessel design and construction.
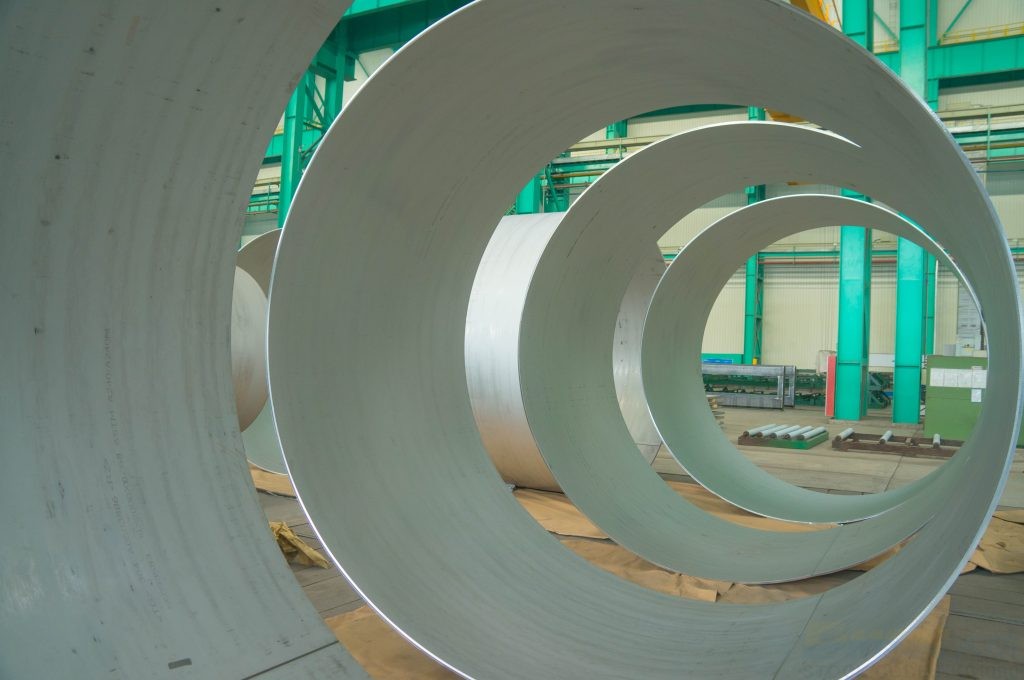
Cost-Effectiveness
Despite the advanced properties and benefits offered by steel, it remains an economically viable option for the oil and gas industry. The cost-effectiveness of steel is derived from its abundant availability and the efficiency of modern steel production processes. Moreover, the durability and low maintenance requirements of steel materials contribute to reducing the total cost of ownership of pressure vessels. These economic considerations are crucial for the oil and gas industry, where budget constraints and the need for cost-effective solutions are ever-present.
In conclusion, steel materials are fundamentally important to the oil and gas industry, particularly in the context of pressure vessel fabrication. The unique combination of strength, durability, corrosion resistance, and flexibility in fabrication, alongside cost-effectiveness, makes steel the material of choice for this demanding sector. As the oil and gas industry continues to evolve and face new challenges, the role of steel in ensuring the safety, efficiency, and sustainability of operations remains undiminished.
The importance of steel in the fabrication of pressure vessels is indeed multifaceted, influencing not just the construction phase but also the long-term operation and safety of these essential components in the oil and gas sector. As technology advances, the marriage between steel materials and pressure vessel fabrication is expected to grow even stronger, ensuring safer and more efficient energy production for years to come.